The packaging industry plays a significant role in ensuring product safety and compliance for manufacturers. Packaging serves as the primary layer of protection for products during transportation and storage, and it also provides essential information about the product to consumers. In this article, we will discuss the importance of packaging in product safety and compliance, and we will explore some of the best practices that manufacturers should follow to ensure their products are safe and compliant.
Importance of Packaging in Product Safety and Compliance
Packaging serves multiple functions when it comes to product safety and compliance. Firstly, packaging provides protection for products during transportation and storage. The packaging should be designed to prevent damage and contamination from external sources such as dust, moisture, and insects. The packaging should also be strong enough to withstand the rigors of transportation and storage, including temperature changes, humidity, and pressure.
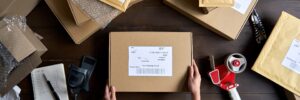
Another crucial function of packaging in product safety and compliance is labelling. Packaging should provide all necessary information about the product, including the product name, ingredients, warnings, usage instructions, and regulatory requirements. Packaging labelling is critical because it helps consumers make informed decisions about the products they are purchasing.
Packaging also plays a vital role in meeting regulatory requirements for safety and compliance. For instance, the packaging for food products must meet the regulatory requirements set by the FDA regarding food safety. Manufacturers must ensure that their packaging materials are compliant with regulations, including the labelling and nutrition information requirements.
Best Practices for Manufacturers
There are several best practices that manufacturers should follow to ensure their products are safe and compliant.
Conduct Regular Audits and Testing of Packaging Materials
Regular audits and testing of packaging materials are essential for identifying potential weaknesses in the packaging that may compromise product safety. Manufacturers must test their packaging materials for strength, durability, and resistance to environmental hazards. For instance, food packaging materials must be tested for resistance to moisture, oxygen, and other external factors that may cause contamination or spoilage of the products.
Stay Up-to-Date with Regulatory Requirements
Regulatory requirements for packaging safety and compliance can vary by industry and region. Manufacturers must stay up-to-date with all relevant regulations and ensure that their packaging meets these requirements. This includes understanding the labelling and nutrition information requirements, material restrictions, and any safety warnings or instructions for disposal.
Work Closely with Packaging Suppliers
Manufacturers must work closely with their packaging suppliers to ensure that the packaging materials used are safe and compliant. Packaging suppliers should provide documentation and certifications to confirm that their materials meet regulatory requirements. It is essential to choose a reputable and reliable supplier that understands the regulatory requirements for packaging safety and compliance.
Incorporate Sustainability into Packaging Design
Sustainable packaging can help to reduce waste and environmental impact while also providing benefits such as cost savings and increased brand reputation. Manufacturers can use sustainable materials, such as biodegradable or recyclable materials, and design packaging that is lightweight and efficient. The entire life cycle of the packaging should be considered when designing for sustainability, including the manufacturing process, transportation, and disposal.Transparency with Customers
Manufacturers must be transparent with their customers about their packaging and the measures they are taking to ensure product safety and compliance. Providing information on the materials used in packaging, the testing and auditing process, and any sustainability initiatives can help to build consumer trust and loyalty.
Emerging Technologies and Innovations
Emerging technologies and innovations in packaging can also play a role in ensuring product safety and compliance. These technologies include:
Smart packaging refers to packaging that uses technology to provide additional functionality beyond basic protection and containment. Smart packaging can include features such as temperature and humidity sensors, tracking devices, and tamper-evident seals. These features can help manufacturers monitor the safety and quality of their products and detect any issues during transportation and storage.
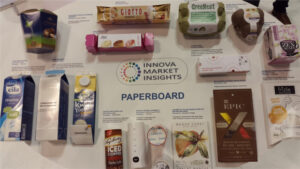
Active Packaging
Active packaging refers to packaging that actively interacts with the product to extend shelf life or enhance safety. Active packaging can include oxygen scavengers, moisture absorbers, and antimicrobial agents. These features can help prevent spoilage or contamination and improve product safety and compliance.
Nanotechnology
Nanotechnology refers to the manipulation of materials on a nanoscale level. Nanotechnology can be used to enhance the properties of packaging materials, such as making them more durable or enhancing their barrier properties. Nanotechnology can also be used to create new packaging materials with unique properties, such as self-cleaning or self-healing properties.
Additional Considerations
In addition to the best practices mentioned above, manufacturers should consider the specific needs of their products and industries when designing packaging for safety and compliance. For instance, packaging for pharmaceuticals must be designed to protect the product from temperature and humidity changes, as well as from tampering and contamination. Similarly, packaging for hazardous materials must meet strict regulations for safety and disposal.
Manufacturers should also be aware of any emerging technologies or innovations in packaging that can help to enhance product safety and compliance. For instance, smart packaging can be used to monitor the temperature and humidity of products during transportation and storage, providing real-time data that can be used to identify potential issues and prevent spoilage or contamination.
In addition to these best practices, manufacturers must also be prepared to adapt to changes in regulatory requirements and industry standards. As new technologies and materials emerge, regulatory agencies may update their requirements, and manufacturers must be aware of these changes to ensure compliance. Manufacturers should also be prepared to address any issues that arise with their packaging, such as recalls or product defects, and take prompt action to address these issues to minimize the impact on consumers and their brand reputation.
Conclusion
In conclusion, packaging plays a crucial role in ensuring product safety and compliance for manufacturers. Packaging provides protection for products during transportation and storage, and it also provides essential information to consumers. To ensure product safety and compliance, manufacturers must conduct regular audits and testing of packaging materials, stay up-to-date with regulatory requirements, work closely with packaging suppliers, incorporate sustainability into packaging design, and be transparent with customers. Manufacturers should also consider the specific needs of their products and industries and be aware of emerging technologies and innovations in packaging that can enhance product safety and compliance. By following these best practices, manufacturers can ensure their products are safe and compliant while also building consumer trust and loyalty.